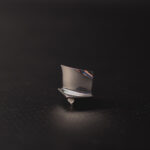
High-Precision Control of Surface Roughness
Precision-engineered parts, such as gas turbine components, leave no room for error concerning surface treatment.
The Micro Machining Process (MMP TECHNOLOGY®) is a surface finishing technology based upon selective filtration of wavelength ranges of roughness, allowing for the production of super precise and selective surface states.
The results are uniform and reproducible: MMP TECHNOLOGY® is an industrial process that ensures total traceability and industrial-grade control of all parameters from start to finish.
MMP TECHNOLOGY® is highly effective on virtually every alloy, regardless of hardness. MMP TECHNOLOGY® can treat parts made from any manufacturing method, including forging, casting, machining, EDM/ECM, and additive layer methods (DMLS, SLM, etc.).
Worldwide the MMP TECHNOLOGY® plants process over a million components of compressors and engines of flying hardware.
Component types
Characteristics
High-Precision Control of Surface Roughness
MMP TECHNOLOGY® is highly effective on virtually every alloy, regardless of hardness. MMP TECHNOLOGY® can treat parts made from any manufacturing method, including forging, casting, machining, EDM/ECM, and additive layer methods (DMLS, SLM, etc.).
Technical Benefits of Using MMP
- Increased resistance to corrosion
- Reduced friction
- Increased resistance to wear
- Improved aerodynamics
- Reduced micro turbulence
MMP Advantages
- Cost and lead times are predictable and tightly controlled
- Homogeneous finishes reproduced to industrial standards for every part
- Treated components exhibit superior technical performance
- Ensures industrial-standard traceability and uses certified quality procedures for key suppliers with a very high service rate
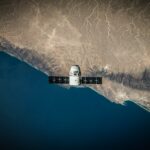
Added Values
MMP TECHNOLOGY® guarantees high-performing, homogenous, reliable parts.
We strive in all of our services to give the best possible satisfaction to our partners and customers.