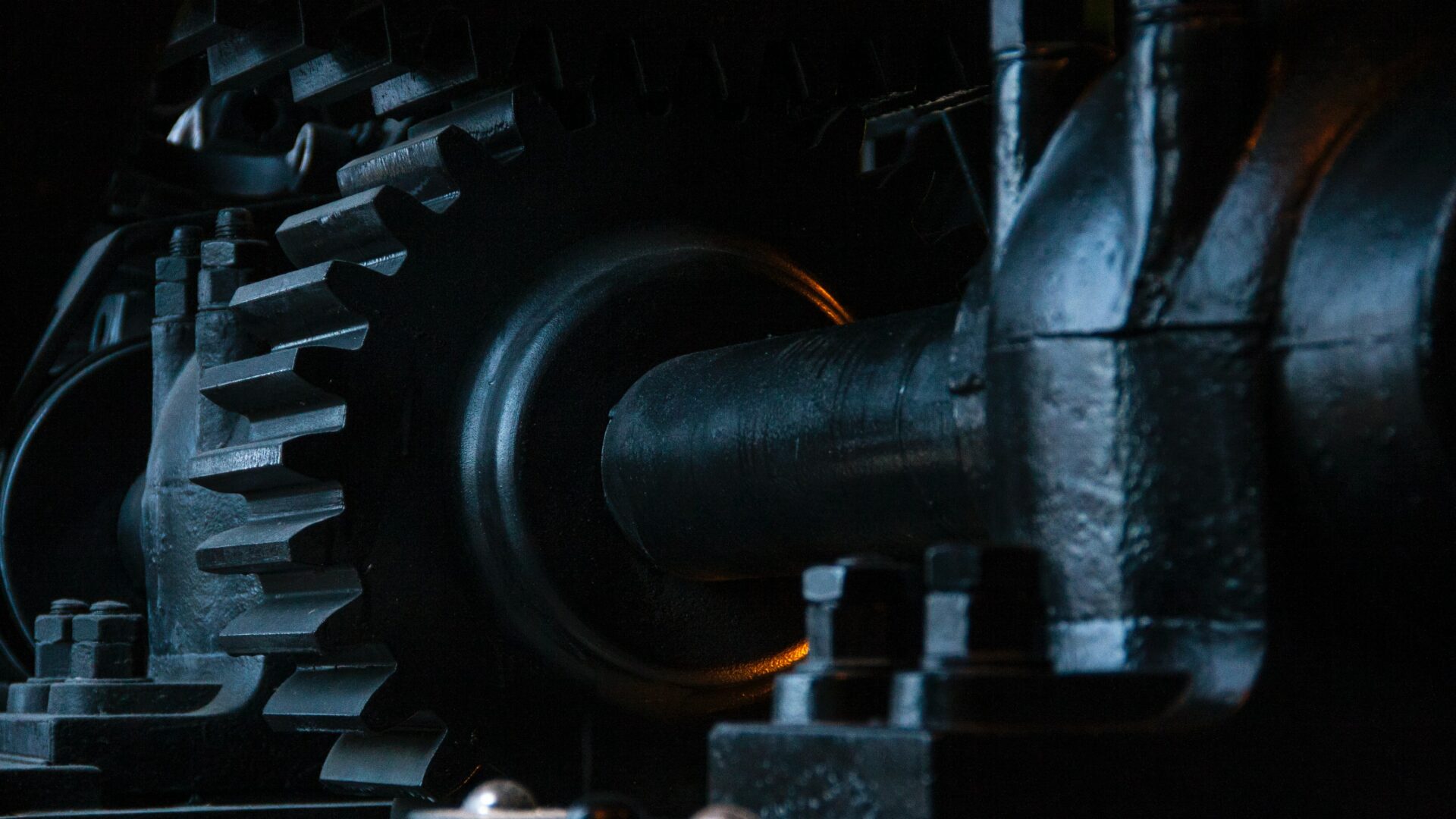
Repair of High Value/High Demand Spiral Bevel Gears by Superfinishing
This paper describes a research and development effort focused on the remediation of high value, high demand spiral bevel gears for the UH-60 helicopter tail rotor drive train. Spiral Bevel gears for the UH-60 helicopter are in generally high demand due to the needs of new aircraft production and the overhaul and repair of aircraft returning from service. This makes the acquisition of new spiral bevel gears to support R&D activities very challenging. These difficulties and the potential for significant cost savings, led to the assessment of an emerging superfinishing process, known as the Micromachining Process or MMP, as a repair technique for spiral bevel gears. The use of superfinishing also was believed to offer potential performance and durability improvements over the existing ground surface finish. Candidate gears were those previously rejected during overhaul for surface damage to the active tooth profile. Candidate rejected UH-60 Tail Take-off (TTO) spiral bevel gears were obtained from Corpus Christi Army Depot. A selection process involving inspection for cracks, and characterization of the surfaces was conducted. Two gears were selected for refurbishment using MMP. Surface replication and detailed coordinate measurements were conducted on the gears both pre and post MMP. One of these gears was then installed into a UH-60 main transmission and subjected to a 25 hr overload test. The results of the MMP process and the performance of the gear are described in this paper.
Eric C. Ames
Aerospace Engineer
US Army Research Development and Engineering Command Aviation Applied Technology Directorate Ft. Eustis, Virginia eric.ames@us.army.mil